Imagine a new manager at a beef packaging plant who knows nothing about the birthing process of calves. On the first day his workers show him a newborn calf. The dollar signs go off in his head as he calculates: more calves mean more beef; more beef means more sales; more sales mean more profits. He points to the mother cow and barks, “I want you to get two more calves out of that sucker by Monday morning, and that’s an order!”
Of course, the workers will find a way to fulfill his request, either by bringing two calves from another part of the plant or perhaps slaughtering the mother cow Stage 1 to produce the extra pounds of beef. The workers will have successfully executed their task, and the manager will continue to believe that his orders control the production cycle of calves.
The story is obviously farfetched. No one would expect a cow to produce a calf in one weekend. But how do we know that equally ridiculous demands are not being made every day on processes where we have less understanding of the time dynamics? Are there such “calving” equivalents in the manufacturing environment, for example, where arbitrary quarterly sales targets given to investment analysts translate into marching orders for the production line?
Aging Chain Structure
Why is it that whenever we want something right away, it seems to take forever? Then when we do get it, it often is more than we ever wanted? Chances are, delays played a large part in our mistiming. We realize that “things take time,” but unless we have a clear understanding of the structure that produces the delays, it is difficult to know how long the appropriate waiting time is before we should take further action.
Whenever there are significant delays in a system, you can bet that there are accumulators involved. In some cases the accumulators are less obvious than in others, but they almost always play a role. In the case of the packaging plant, the accumulator is the cow (or stock of cows). When taking a shower, for example, the delay in getting hot water is due to accumulation in the length of pipe from the hot water heater to the shower. Even though the water “flows” through the pipe, the volume of water in the pipes can be viewed as an accumulation of cold water being pushed through the pipes by the subsequent hot water.
Generic Aging Chain Structure
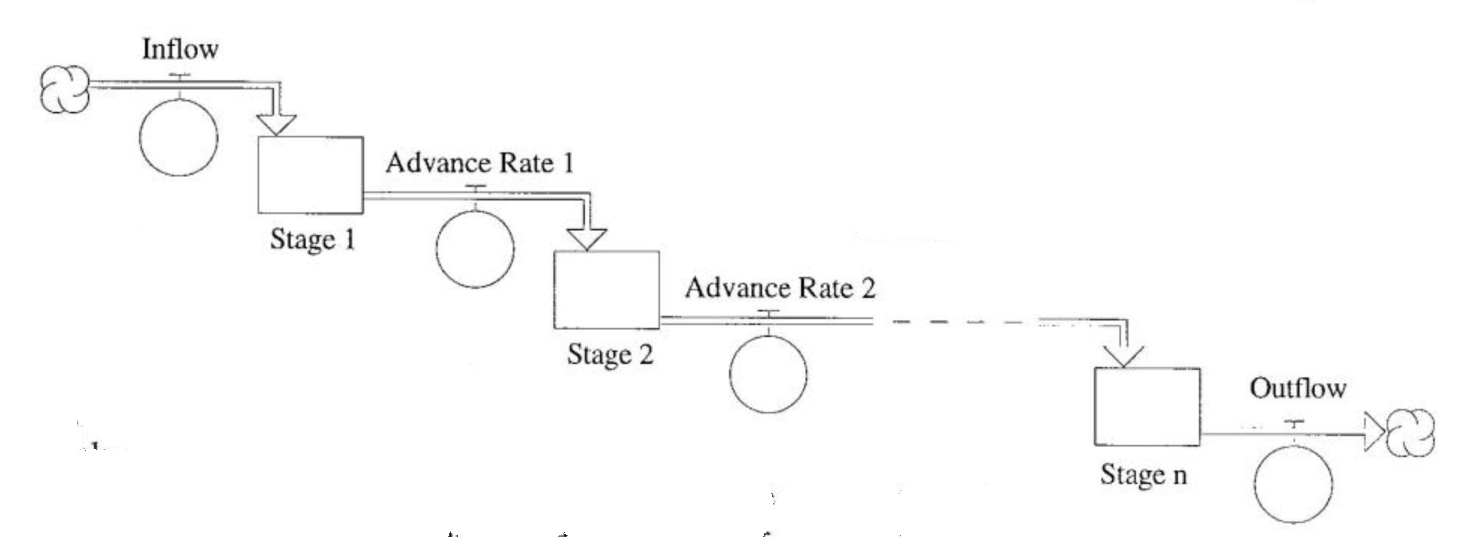
The “aging chain” structure represents a multi-stage process where “stuff” moving through the system undergoes various stages of development (indicated by accumulators).
The “Aging Chain” structure is the name given to a whole class of processes that includes the birthing cycle of cows, production-distribution systems, and the spread of infectious diseases (see “Generic Aging Chain Structure”). The key principle in the Aging Chain is that there are delays in the system that depend on the inherent nature of that system, and those delays cannot be shortened except within some narrow bounds. For calf production that delay is the gestation period. For new ideas it may be an incubation period, for new products it may be the development time, and for production it is the manufacturing cycle time. Trying to shorten the inherent time delay by pushing things through the accumulators faster can wreak havoc on the system.
The aging chain represents a multistage process where “stuff’ (ideas, products, calves) moving through the system undergoes various stages of development. Each stage can be represented by an accumulator, where the stuff “ages” before moving on to next stage, and the “aging” time at any stage can vary.
Production Systems
One way to get a better idea of the delays involved in a system is to create a structural map. A typical production system is shown in the “Production Chain” diagram. In the diagram, different stages of production process are represented by accumulators (for dimensional consistency, this diagram represents accounting numbers and not the actual physical stuff moving through the system). The accumulator and flow diagram is very much like a process flow chart, showing how production can be mapped out as a series of stages. Each accumulator, in effect, adds a delay into the system.
If we wanted to add greater detail, each accumulator could be further broken out into smaller stages. For example, the Work in Process accumulator may be broken into various production stages such as assembly, paint, hake, test, and inspection. Each stage has its own time delay or cycle time associated with it.
An important aspect of these time delays is that they usually do not stay constant — a point that is not captured in a typical process flow chart. In the first stage, for example, a rising backlog of production requests increases the scheduling load which decreases the rate at which the requests can be scheduled. This keeps the backlog high, further exacerbating the schedule load problem (RI). Once a schedule gets behind, the system can actually reinforce the tendency to fall further behind.
Production Chain
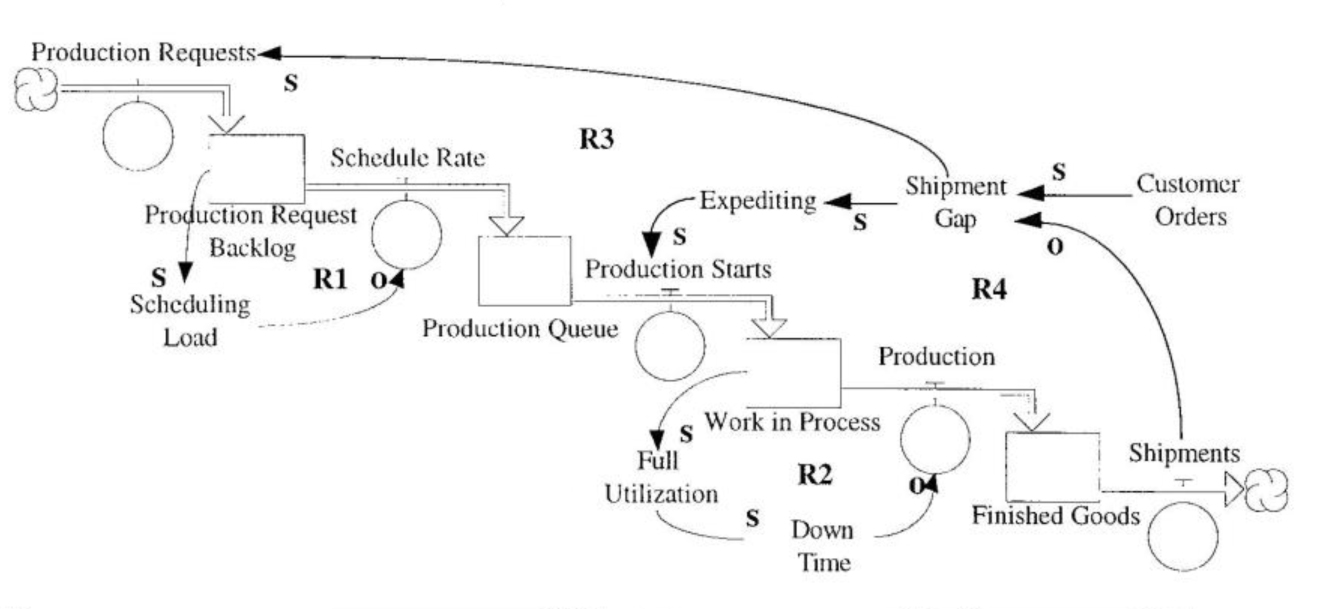
Each stage of the production chain flow diagram has its own time delay or cycle time associated with it. In many cases, the length of tune changes as a function of the system — a point that is usually not captured in a typical process flow diagram.
Expediting Loops
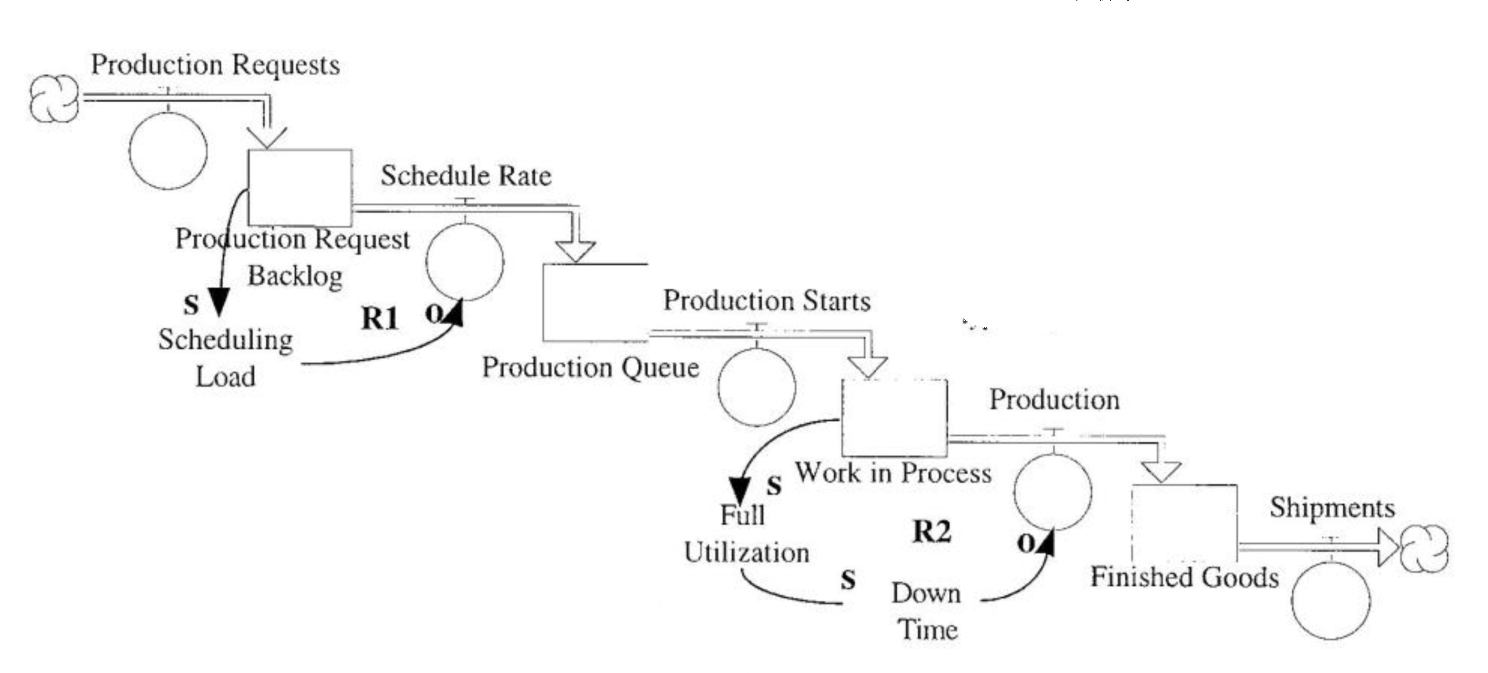
Efforts to expedite orders can backfire by actually lengthening the average production delay and reinforcing the need to expedite (loops R3 and R4).
Don’t Just Do Something, Stand There!
The “Production Chain” diagram does not show the complete picture of what goes on in a typical manufacturing setting (see “Expediting Loops”). When shipments fall short of customer orders, the result is that customers are left waiting for their goods. One response to such a gap is to go into the production system and expedite some of the more “important” orders and/or push more production requests into the system. The intent is to get more products through the chain, but these actions are likely to produce the opposite effect.
Given that the system was already running at full tilt, the expediting actions are likely to create additional reinforcing sources of delays. Pushing on production requests will kick in the scheduling load loop (RI), which will further delay shipments and put additional pressure to expedite (R3). Similarly, rearranging the production starts and pushing orders into production will exacerbate the full utilization loop (R2), leading to further delays and more pressure to expedite (R4).
In general, the aging chain structure tells us that there are structural limits to how fast you can force a system to respond. Unless you can somehow change the inherent delays built into the various stages of the system, the best expediting action one can take may be to simply do nothing — and wait.