Many companies are pursuing registration to the international Quality System Standard known as ISO 9000. This standard is based on a quality model used by the British military and is akin to the U.S. military standard Mil-Q-9858A. ISO 9000, and related standards like QS 9000 (for the automotive industry), lay out specific requirements for creating and maintaining a documented “quality system.” These requirements include written policies and procedures and documentation in areas such as management responsibility, contract review, design control, document/data control, purchasing, corrective and preventive action, auditing, training, and so forth. In all, there are 20 main areas that must be documented if a company is to show ISO/QS compliance.
To enter the program, a company sets up a system that complies with the standard, operates for a while to prove that the system works, documents progress, and has a qualified registrar audit the system and recommend the firm for registration. Not surprisingly, this process gets pricey. It can cost $5,000 to $20,000 to register, and anywhere from $30,000 to $100,000 per year to maintain the new system.
Any company pursuing formal registration to the standard must maintain a regular schedule of “compliance audits.” At such audits, the company provides documented proof that both the quality system design and function comply with the standard. The audit program includes a regular schedule of internal audits (self-evaluation) and audits by a qualified external source (known as a third-party registrar). These audits take place regularly for as long as the company chooses to maintain registration. Through this process, registered companies can “say what they do and do what they say.”
Companies usually choose to register for ISO/QS compliance in response to customer requirements. In addition, the standard gives organizations an opportunity to continually improve their processes, the reliability of their products or services, the quality of relationships with their customers, and, ultimately, profitability (see “What We Hope For”).
WHAT WE HOPE FOR
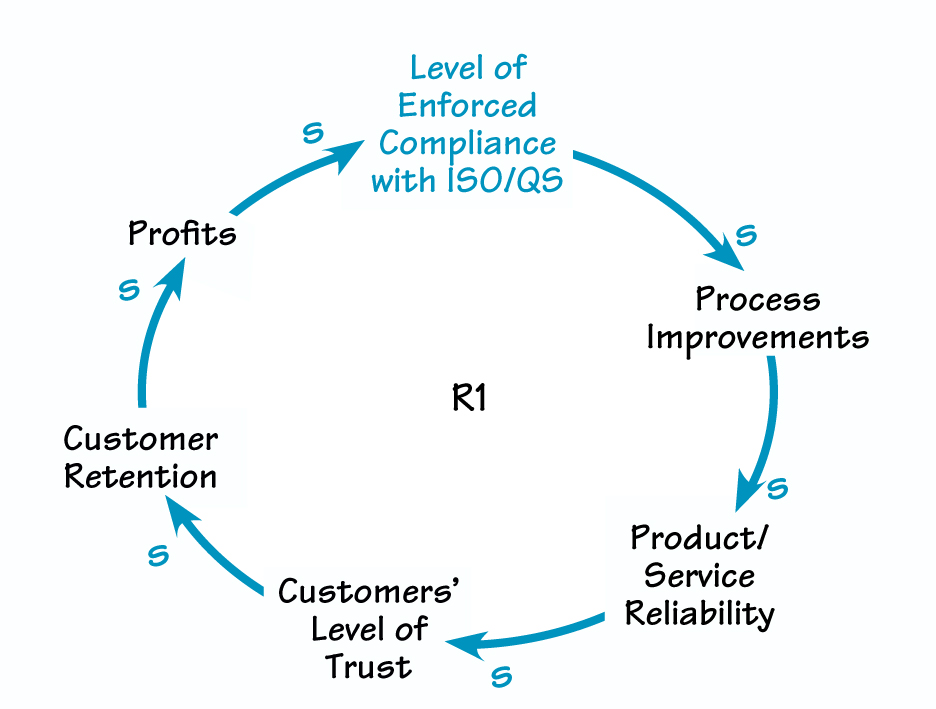
Some companies registering for ISO/QS 9000 hope that compliance with the standards will lead to improved processes, product/service reliability, relationships with customers, and ultimately profitability.
Mixed Reviews
Many people swear by these standards as a great way to set up a basic quality system. Such advocates claim that proper implementation can repay the cost of becoming registered many times over. Numerous books have also proclaimed the value of pursuing registration to the ISO/QS standards.
Yet there are also many detractors who argue that these standards are worse than inadequate. The standards, they lament, do not necessarily catalyze positive change. These critics point out that a company can become registered by merely documenting a poor system. As one wit put it, “You could make life preservers out of cement and get registered — as long as you document your system.” Some claim that enforcing standards like ISO actually impedes adaptability by encouraging an explosion of paperwork, “red tape,” and bureaucracy. One author published a book about ISO 9000 in England, where 50,000 companies are registered, some for as long as 20 or more years. His conclusion: that every one of the 50,000 companies, and the British economy in general, has suffered serious and permanent harm as a result of ISO 9000.
Determining which (if either) side is right will probably take another 20 years. As with many complex questions, the truth will likely turn out to be somewhere between the two extremes.
Questions for Reflection
- What might be some unintended consequences — both short-term and long-term — of vigilant compliance with these standards?
- How might unintended consequences feed back in such a way as to limit any gains achieved by compliance to the standards?
- How might feedback delays within the system influence the results of complying with ISO/QS standards?
Visibility Works
“Visibility Works” is a systems thinking principle that has an important implication: It assumes that, if we can work together to create a theory about what might be happening in a system over time, we have the potential to influence the outcome of those dynamics in desirable ways. By creating a visual depiction, we can identify “leverage points,” or better yet, perhaps even alter the dynamic structure itself so that it yields more positive outcomes.
How might the tools of systems thinking help us to visualize the dynamics involved in becoming registered to ISO/QS 9000? Causal loop diagrams are one way of graphically developing our hypotheses. Our intent in using such visualization would be to identify ways to maximize the potential benefits of registering and minimize the potential downsides. In sketching out a diagram, we would want to pay particular attention to shifting dominance of certain loops (see Dennis Meadows’ “Breaking the Cycle of Organizational Addiction,” V8N7). This exercise is valuable for three reasons:
- As we’ve seen, seeking formal registration to ISO/QS 9000 is a serious challenge and costly in terms of time and effort.
- The more powerful the tool (in this case, the ISO standard), the greater the potential for benefit (if used correctly) and harm (if used incorrectly).
- Registering is becoming a requirement for many businesses, owing to the markets and customers they have chosen to serve.
With these concerns in mind, let’s explore the dynamic structures that might be involved in registering in ISO/QS 9000, and particularly in maintaining registration over time.
Looking at Dynamic Structure
There are five key feedback structures worth considering for any organization that may be wondering whether to register for ISO/QS 9000. We already looked at the first one, “What We Hope For” (R1). Let’s now expand the picture:
“Cost Savings.” When the reliability of products and services goes up, the internal and external failure costs (scrap, rework, warranty, etc.) should go down (R2) (see “Reinforcing Processes).
REINFORCING PROCESSES
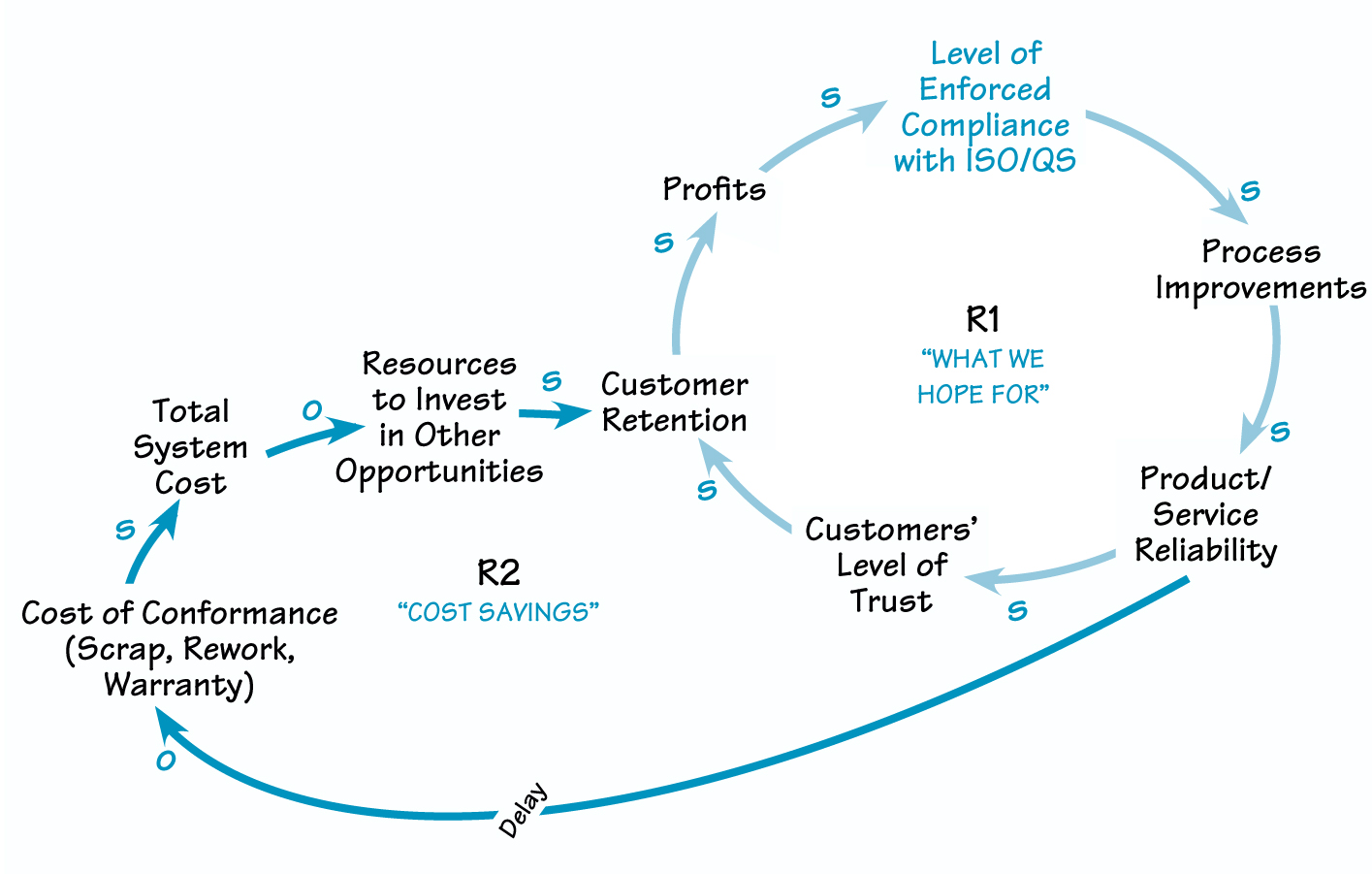
In addition to improving processes, product/service reliability, and customer relations, conforming to ISO/QS standards can lead to cost savings and money to invest in other opportunities.
However, there can be a delay in realizing these savings, because it takes time for the added reliability to make a difference. This is a classic “worse before better” dynamic, which can cause stress within the organization when improvement efforts don’t immediately pay off. When failure costs finally go down, pressure on the total system cost is relieved and more resources are made available to invest in other opportunities. As long as this cost savings loop is stronger than the investment loop (B3), the impact on the customer/supplier relationship is positive overall.
“Investment.” As the level of enforced compliance to ISO/QS standards goes up, the cost of compliance also goes up, owing to corrective actions, system maintenance, etc. (see “Five Loops”). This expense can increase cost pressures on the total system and take investment resources away from other opportunities. If this loop should begin to dominate, it would reverse any gains achieved from boosting customer retention and profits.
“Bureaucracy.” The increased level of compliance to ISO/QS standards that occurs as audits continue over time can lead to more and more bureaucracy (B4). Bureaucracy can in turn result in increased rigidity throughout the organization, whereby the firm becomes less adaptable to rapidly changing customer and market needs. Not surprisingly, lack of responsiveness to customers can severely damage customer retention over time.
“Employee Motivation.” Too much of a focus on “problems” (what’s not working) as opposed to forward movement (what is working, or what we need more of to achieve our purpose) can seriously corrode employee moral, motivation, and willingness to embrace change (B5). The primary focus of auditing (enforced compliance) is on finding what is known as “non-compliances”; for example, failure to calibrate a measuring device (minor non-compliance) or failure to have a functioning calibration program (major). Third-party, professional auditors typically discover anywhere from a dozen to 50 or more non-compliances every time they perform an audit. Most auditors would not consider that they had done their job well unless they uncovered a “respectable” number of non-compliances.
Regardless of how hard a company may try to couch such “findings” in terms of opportunities, this kind of auditing is unavoidably problem-focused. Often, the relationship between auditor and auditee ranges from wary to downright adversarial. Over time, this tension can drain the organization’s positive energy, leading to lower motivation and damaged morale. If motivation and morale go down, customer service could suffer, which in turn could threaten customer retention.
FIVE LOOPS
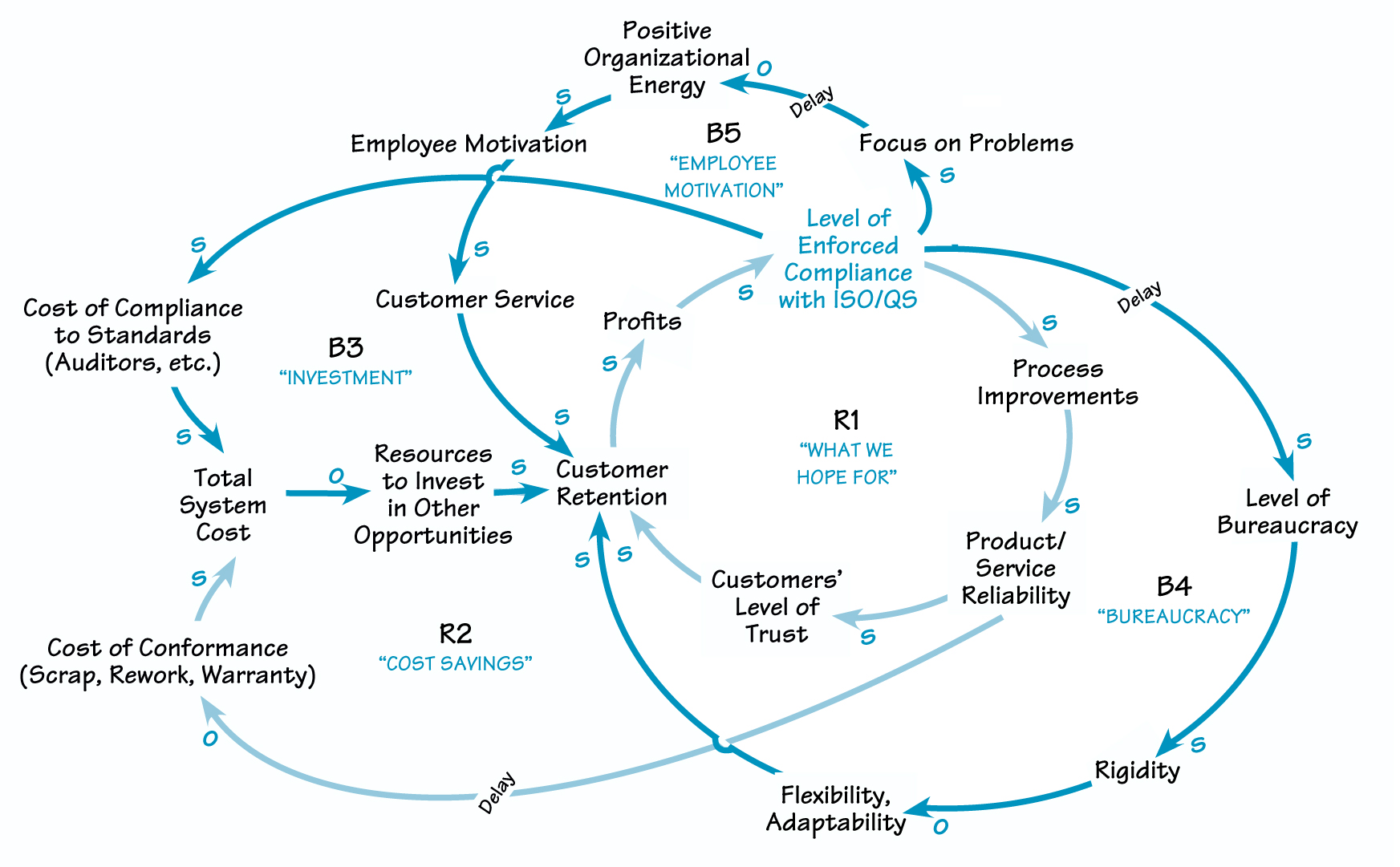
The positive reinforcing cycles of compliance to ISO/QS standards, improved customer/supplier relationships, and cost savings (R1 and R2) may be balanced by the negative impacts of increased costs of compliance (B2), an unavoidable rise in bureaucracy (B4), and a focus on problems brought about by incessant auditing (B5).
Using the Learning
The kind of diagram explored above offers a number of important benefits:
Heightened Awareness. Working to create a causal loop diagram can help make people more sensitive to the issues of balancing the costs and benefits of ISO/QS, avoiding the pitfalls of bureaucracy and red tape, managing the “worse before better” dynamic, and understanding the potential dangers of a narrow focus on problems. Equally important, the diagram shows the potential value of the ISO/QS standards — for both product/ service reliability and cost control — if compliance is implemented carefully.
Action Planning. After studying the causal loop diagram, a company could take specific actions, such as measuring the cost of maintaining registration against any reduction in internal and external failure costs. Organizations could also design strategies — for example, to focus more energy on key areas that are working well or to simplify and minimize paperwork, so as to avoid becoming overly bureaucratic or problem-focused. Another key leverage point is to find ways to realize the potential benefits (specifically, the cost savings) of product or service reliability. For example, an organization could carefully measure and analyze costs associated with scrap, rework, warranty, and other wastes to justify focused improvements. Finally, companies could use visual tools, such as a responsibility matrix and a Balanced Scorecard, to assess progress in the planned action areas and measure cost savings.
“Visibility Works” — the idea that creating a graphic representation of systemic behavior can help us fine-tune the system for more positive outcomes — is a powerful concept for any organization seeking to implement complex changes in its business systems. The tools of systems thinking can be useful devices for visualizing complex dynamics. However, real results still occur only when people act on the insights gained from such tools.
NEXT STEPS
- Gather a group of people who know your company’s quality system and the ISO/QS 9000 standards. Together, construct a causal loop diagram that describes the feedback loops and delays in your system.
- Analyze the dynamics, including how they will play out over time. Search for systems archetypes, such as “Drifting Goals,” “Escalation,” “Fixes That Fail,” etc.
- Design a plan to minimize or avoid undesirable “loops,” such as “creeping bureaucracy,” “costs exceeding benefits,” “too much focus on problems,” “audit anxiety,” and so on. Include specific actions, timing, and assigned ownership in the form of a visual responsibility matrix.
Dennis Grahn is director of Quality at Menasha Corporation. Lauren Keller Johnson is publications editor at Pegasus Communications.