In our efforts to develop empowered workplace teams, we need dialogue tools to support productive, “no-blame” conversations about performance issues. My colleagues and I have found one tool, the Pocket Matrix developed by Shigehiro Nakamura at the Japan Management Association, particularly useful as a framework for holding productive conversations between managers and employees and among team members. Although Nakamura designed the Pocket Matrix as an improvement tool for use in a manufacturing environment, organizations in other industries can easily adapt it to suit their own needs.
The Pocket Matrix
The Pocket Matrix is a simple two-dimensional grid that lists the inputs and outputs of the manufacturing process. The facilitator puts the inputs on the vertical axis of the matrix. These categories follow a familiar model commonly used with problem-solving tools such as Fishbone Diagrams, known as the 6Ms: Materials, Machines, Measurements, Methods, Men/Women, and Management Information.
On the horizontal axis, the outputs include Quality, Cost, Delivery, Safety, and Morale (QCDSM). QCDSM is an almost universal language in the automotive and electronics industries for discussing business targets. Many manufacturers now include E for Environment as an output as well.
This input/output model gives teams an explicit framework for sharing their mental models of the manufacturing process. Nakamura called this tool the “Pocket Matrix” or “Idea Bank” because each square on the matrix is a “pocket” in which we can collect comments, ideas, and suggestions. Teams use the Pocket Matrix to focus their discussions and create a profile of areas for improvement in a business line.
In our efforts to develop empowered workplace teams, we need dialogue tools to support productive, “no-blame” conversations about performance issues.
To begin the process, the facilitator gives participants cards or Post-It® notes and asks them to write down any concerns or observations they have that relate to difficulties in achieving the required outputs of QCDSM. He or she then draws a copy of the matrix on a flip chart. The group members stick their comments on the matrix according to where they seem most relevant. Each participant submits one card at a time. The facilitator goes around the group until everyone is out of cards.
For instance, the comment “This job is too tiring” might go in the block that forms the intersection of Men/Women and Morale (see “Sample Matrix” on p. 7). “This machine keeps breaking down” would go into the Machine/Delivery pocket; “This process does not produce satisfactory results” would go into Measurements/ Quality. Groups find it easy to identify the output, but sometimes struggle with the input categories if they have not used them before. The facilitator must emphasize that there aren’t any “right” answers; the important point is to surface people’s assumptions about the causes of their problems.
The patterns of comments that end up on the chart reveal the areas of challenge for that particular work group. Viewing the matrix lets team members make observations such as, “We seem to have a lot of delivery problems stemming from our lack of standardized methods” or “We have quality problems because our measurement systems are inadequate.” Because the observations come from an analysis of a common pool of data, this tool helps teams reach consensus about the issues that face them.
Once group members identify a problem area, they can begin to come to agreement about possible interventions. They might perceive the need for technical training in a particular process; for support in applying a particular improvement approach, such as Poka-Yoke (Mistake-Proofing) for assembly errors; for changes in work methods and structures; or for coaching in the skills they need to solve their particular problems. This process often proves more effective than topdown improvement programs imposed by management, because the team feels a sense of ownership for the solution.
To support dialogue between management and shopfloor teams, facilitators can then have managers perform the same exercise, but using different colored Post-Its. Where a shopfloor team may come up with safety and morale issues, management may focus on cost and quality. By making assumptions visible, offering participants a common language, and shedding light on disparate perspectives, the matrix can help the two groups engage in a constructive dialogue.
This process requires management to behave authentically and to accept that concerns expressed by shopfloor workers are similarly valid. The advantage of using the matrix is that it separates the data from the person, helping participants avoid falling into defensive routines. To use the Pocket Matrix effectively, participants also need to be able to summarize their observations without assigning blame for the problem. The facilitator must make this requirement clear from the start. If the organization’s culture has supported blaming in the past, the facilitator can use a humorous device called the “No-Blame Clock.” The clock continues to tick until someone engages in blaming behavior. Team members try to keep the clock ticking longer and longer each time.
Other Applications
In addition, we have found the Pocket Matrix to be a useful diagnostic tool for teams looking for direction for their improvement activities and for ensuring that improvements are focused on customer needs. Participants find it easy to talk using the terms listed on the two axes of the matrix, although the 6Ms can be confusing if facilitators do not fully define the terms. We encourage groups to work on Management Information, Methods, and Men/Women problems first, as these are more often under the control of the group than more technical solutions that require external resources.
Other modifications of the matrix include replacing the outputs with the company’s own measurement system; for example, a business might set targets in terms of Inventory, so we might use this output instead of Cost. In place of the 6Ms as inputs, we might list the improvement tools and approaches the group is currently using. In this way, teams can see which techniques they have at their disposal for solving their most pressing problems.
Non-manufacturing organizations might want to replace some of the input categories as appropriate. Work methods, people, management information, and equipment would still be relevant for most organizations, as would be the outputs of QCDSM. Some companies might interpret Quality in terms of customer satisfaction scores and Delivery in terms of information processing delays. In fact, some knowledge and service-based businesses might view their offices as information factories, with the same issues of storage, transportation, delays, and so on that manufacturers face.
The Pocket Matrix helps us see work as a process, with certain standard categories of inputs and outputs. Sharing this model enables groups to collect and analyze data about their process and focus on their improvement needs. It helps teams avoid a “flavor of the month” approach to improvement and also helps identify training needs. Above all, this framework gives us a way of talking about challenging issues in a productive, nonthreatening way.
Malcolm Jones has been researching and working with companies implementing World Class Manufacturing techniques since 1986. He founded Productivity Europe in 1989 in partnership with Norman Bodek, founder of Productivity Inc. in the USA. Since 1993, he has been working closely with the TP Management group at the Japan Management Association and has spoken at manufacturing conferences in the U. K., U. S., and Japan.
SAMPLE MATRIX
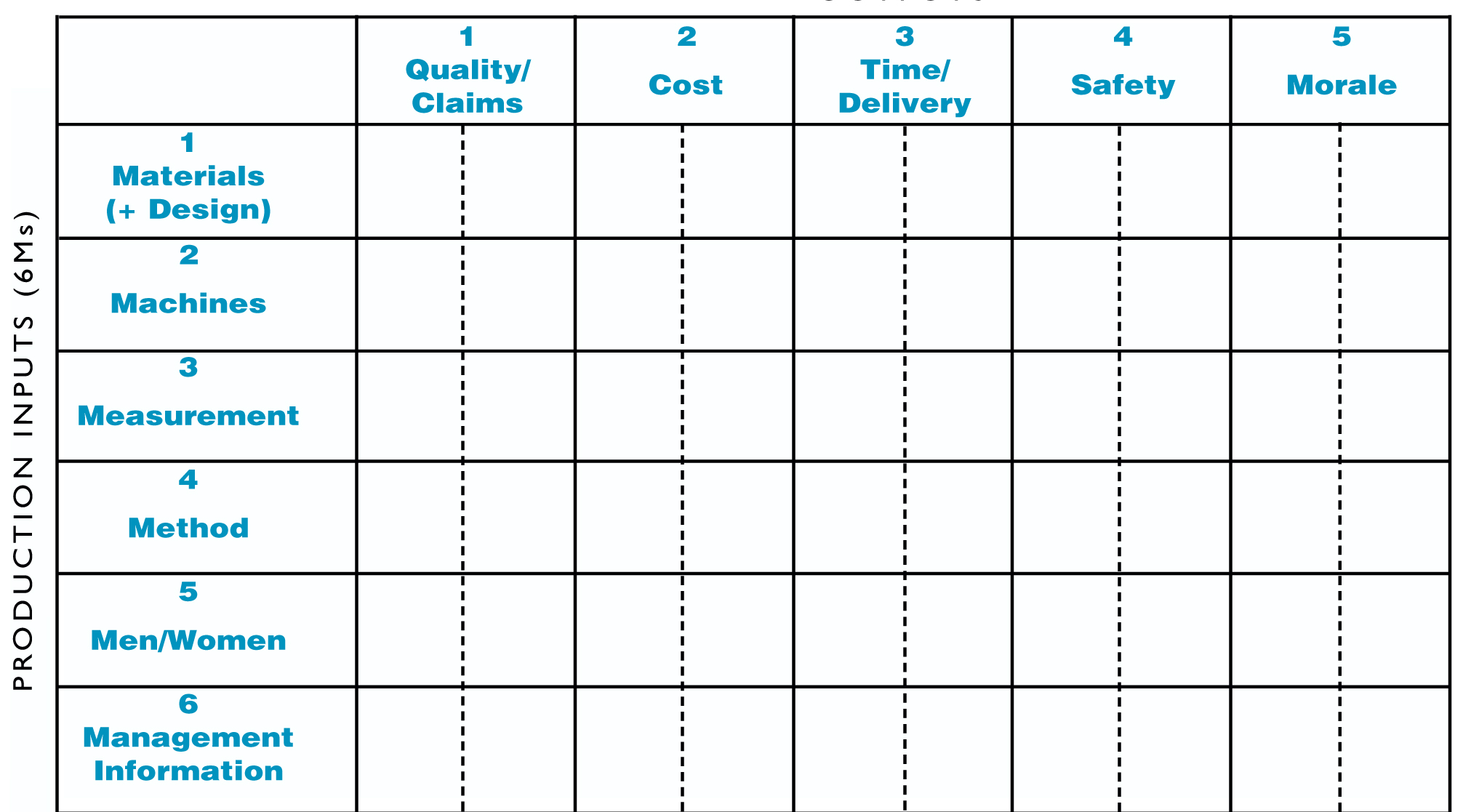
This input/output model gives teams an explicit framework for sharing their mental models.